3Dプリンター部品製作のメリットとポイント|製造業での活用法
- 合同会社HANDA
- 3 日前
- 読了時間: 18分

▶︎1. 3Dプリンターによる部品製作の魅力とは?

1.1 3Dプリンター部品製作の基本とメリット
3Dプリンターによる部品製作は、設計データをもとに素材を積層して成形する技術です。従来の切削加工とは異なり、材料を削るのではなく「積み上げて」形を作るのが最大の特徴です。
この方式によって、複雑な形状の部品も一体成形で作れるのが大きなメリットです。
設計から製作までのスピードが早く、少量生産にも柔軟に対応できることから、試作段階や個別カスタマイズのニーズにもぴったりです。
3Dプリンター部品製作の主なメリット
たとえばこんなメリットがあります。
コスト削減
金型が不要なので、初期投資を抑えられます。1点モノの製作でも無駄がありません。
納期短縮
設計データがあれば即日造形も可能。量産前の検証がスピーディに行えます。
軽量化・最適化設計ができる
従来の加工方法では難しかった中空構造や格子形状の部品も作れるため、製品の性能向上につながります。
よくある失敗例とその対策
3Dプリンターは便利な反面、慣れていないと失敗も起こりやすいです。特に初心者がつまずきやすいポイントとしては以下のようなものがあります。
形状がうまく出ない(積層エラー)
→ 原因はデータの不備や積層方式の選定ミス。STLデータの確認とスライス設定の見直しが必要です。
素材選びに失敗する
→ 熱に弱い素材を選ぶと、耐久性が不足することがあります。使用環境に適した樹脂・金属の選定が大事です。
設計通りに出力されない
→ 熱収縮や支持材の影響で精度に差が出ることも。試作段階で実際の形状確認を行い、逐次修正する姿勢が求められます。
日常シーンでのメリット実感
たとえば、製造現場で「もう少しだけ形状を変更したい」という要望が出た場合でも、設計データを修正すれば即座に反映可能です。 これまで2週間かかっていた調整作業が、3〜4日に短縮されるケースも珍しくありません。
この柔軟性とスピード感こそが、3Dプリンターを活用した部品製作が注目されている理由です。
1.2 3Dプリンターで製作できる部品の種類
3Dプリンターでは、用途に応じてさまざまな種類の部品を製作できます。設計の自由度が高く、従来の加工では難しかった形状にも対応可能です。
製品試作から治具、最終製品の一部まで幅広く活用されているのが特徴です。
素材や造形方式によって適した部品が変わるため、目的に応じた選定が重要です。
よく使われる部品のカテゴリー
3Dプリンターで製作される部品は、以下のような目的で活用されています。
試作部品(プロトタイプ)
新製品開発の初期段階で形状や機能を確認するために用いられます。複数回にわたる改良がしやすく、開発スピードが上がります。
治具・工具類
組み立て作業の補助や測定用途で使用されることが多く、現場のニーズに合わせたカスタマイズがしやすいです。
筐体・ケース類
電子部品のケースやカバーなど、外装パーツの製作にも活用されています。小ロットでも高精度に仕上げられます。
最終製品の構成部品
軽量で耐久性のある素材を使えば、実際に製品の一部として使われるケースも増えています。
部品ごとの素材選定の注意点
部品の種類によって、適した素材や造形方式は変わります。ここではよくある選定ミスとその対策を紹介します。
機能性を重視せずに素材を選ぶ
→ 外見だけで判断すると、使用中に割れたり変形したりすることも。強度や耐熱性を重視しましょう。
高精度を求める部品に不向きな方式を使う
→ 微細なパーツをFDM方式で作ると、精度が足りず形状が崩れることがあります。SLAやSLS方式が適しています。
複雑形状に対応できないプリンターを使う
→ サポート材の除去が難しい設計は、構造的に工夫が必要です。設計段階から考慮しましょう。
現場での導入事例に見る利便性
たとえば、毎日のように使う治具が破損した場合、外注で再製作すると数日〜1週間かかることもあります。 3Dプリンターがあれば、その場で設計して数時間以内に再生産できるため、現場の生産性が下がるリスクを大きく減らせます。
こうしたスピード感と柔軟性が、日常的な部品製作に3Dプリンターを導入する最大の理由といえるでしょう。
▶︎2. 3Dプリンター部品製作に必要な機材・ソフトと選定基準
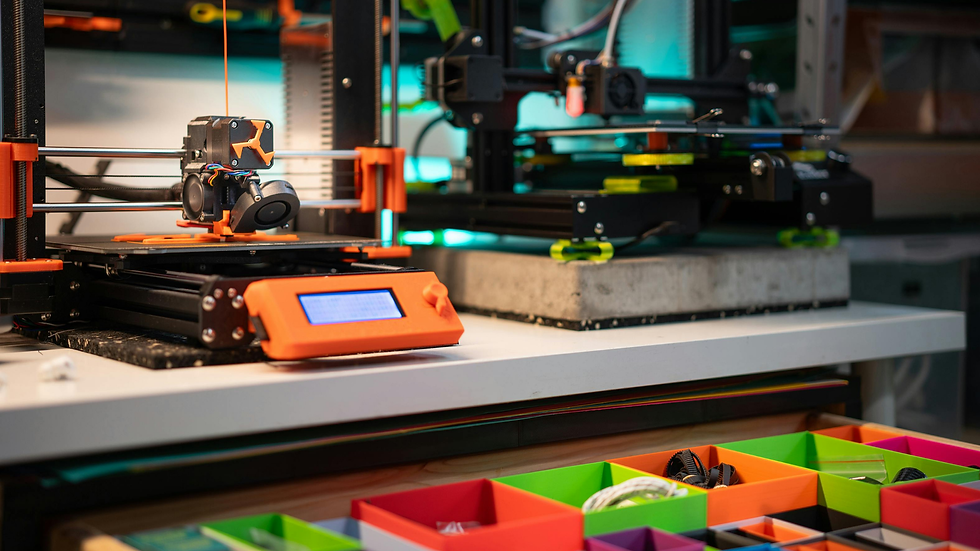
2.1 主要な3Dプリンターの種類と特徴
3Dプリンターにはいくつかの造形方式があり、それぞれに得意・不得意があります。部品の用途や精度、素材に合わせて適切な機種を選ぶことが、製作成功のカギです。
間違った方式を選んでしまうと、精度不足や造形失敗につながるため、選定はとても重要です。
主な3Dプリンターの造形方式
3Dプリンターの代表的な方式は以下の通りです。
FDM(熱溶解積層方式)
熱で溶かしたフィラメント(樹脂)を積み上げて成形する方式。低コストで扱いやすく、試作や簡易治具に向いています。
SLA(光造形方式)
液体レジンにレーザーを照射して硬化させる方式。高精度な仕上がりが特徴で、外観重視の部品や微細な構造に最適です。
SLS(粉末焼結方式)
ナイロンなどの粉末素材をレーザーで焼結して成形。サポート材不要で複雑な形状にも対応でき、実用部品の製作に向いています。
MJF(Multi Jet Fusion)
粉末素材にインクを噴射し熱で焼結させる新方式。量産向けで、表面品質や強度に優れています。
失敗しやすい選定パターンと対策
多くの現場で起きがちな選定ミスには、次のようなものがあります。
価格だけで選んでしまう
→ FDMは手頃ですが、精度や強度が不足する場合も。コストと品質のバランスを見極めることが大事です。
必要以上に高性能な機種を導入する
→ 高額な機種を選んでも、用途に合わなければ無駄になります。必要なスペックを明確にしましょう。
扱える素材が限られていることに気づかない
→ 機種によっては特定の素材しか使えないこともあります。素材対応表を事前に確認することが必要です。
使用シーンごとの機種選びのコツ
たとえば、現場で頻繁に作り替える冶具であれば、FDMタイプの3Dプリンターで十分対応可能です。 一方で、外装パーツや精度が要求される構造部品を作る場合は、SLAやSLSを選ぶと安心です。
用途に合った方式を選ぶことで、トラブルの少ない効率的な運用が実現します。
2.2 3Dデータ作成ソフトの種類と選び方
3Dプリンターで部品を製作するには、まず設計データが必要です。この設計には3D CADソフトやスライサーソフトといった専用ツールが欠かせません。
データ作成の精度が、そのまま部品の品質に直結するため、ソフト選びは非常に重要です。
主な3Dデータ作成ソフトの種類
3Dプリンター関連で使われるソフトには、主に以下の2種類があります。
3D CADソフト(設計ソフト)
部品の形状や寸法を設計するためのツールです。寸法精度の高いモデル作成が可能で、エンジニア向けのものが多いです。
スライサーソフト
CADデータ(通常はSTL形式)を3Dプリンターが読み取れる形式に変換し、積層の指示を出すためのソフトです。積層高さや速度、サポート材の有無などを設定します。
よくあるソフト選びの失敗とその対策
ソフトの選定でもありがちなトラブルがあります。以下のような点には注意が必要です。
操作が難しすぎて使いこなせない
→ 高機能なCADソフトは学習コストも高め。使う人のスキルに合わせたレベル感が大事です。
スライサーソフトとの互換性がない
→ CADとスライサーの連携がうまくいかないと、エラーが多発します。同一メーカー製や連携確認済みのソフトを選ぶと安心です。
設定項目が多すぎて出力ミスが発生する
→ スライサーでは積層ピッチや充填率など細かい設定が多く、間違うと形状不良の原因になります。初期設定をベースに少しずつ調整していきましょう。
シーン別ソフト選びのポイント
たとえば、寸法精度が求められる機械部品を設計するなら、寸法入力が得意なCADソフトを選ぶのが最適です。 一方で、見た目を重視するプロトタイプや試作モデルでは、操作性重視の直感的なソフトの方が作業効率が上がります。
スライサーについても、機種ごとに推奨ソフトがあるため、プリンター本体との相性を最優先に選ぶことがトラブル防止につながります。
▶︎3. 3Dプリンター部品製作のプロセスとポイント

3.1 設計から製作までの流れ
3Dプリンターを使った部品製作には、いくつかの工程があります。流れを理解しておくことで、トラブルや無駄を減らし、効率よく高品質な出力が可能になります。
事前の準備がしっかりしていれば、試作〜完成までの時間を最大で半分以下に短縮できます。
3Dプリンター製作の基本フロー
3Dプリンターによる部品製作は、一般的に以下のようなステップで進みます。
設計(CADモデリング)
3D CADソフトで部品の形状を設計します。寸法や構造に間違いがないよう慎重に確認しましょう。
STL形式でエクスポート
CADで作ったデータを、3Dプリンターが読める形式(STLファイル)に変換します。面の滑らかさもこの段階で決まります。
スライサーソフトで設定
スライサーソフトにSTLデータを読み込み、積層ピッチ、サポート材の有無、充填率などを細かく設定します。
造形(3Dプリンターで出力)
設定が完了したら、プリンターにデータを送り出力開始。造形にかかる時間は部品のサイズや方式によって異なります。
後処理(サポート材除去・研磨など)
造形後、不要なサポート材を取り除いたり、表面を滑らかにするための後処理を行います。
トラブルを避けるための注意点
製作工程では、以下のようなミスや見落としがよくあります。
STL変換で形状が崩れる
→ 曲面の多いデータではポリゴン数が不足するとガタガタになります。エクスポート時の精度設定に注意しましょう。
スライス設定のミス
→ 積層ピッチが粗すぎると表面が荒くなります。0.1〜0.2mm程度の設定が標準的です。
出力中のフィラメント詰まり
→ 長時間の出力ではノズル詰まりが起きやすく、事前の清掃や素材チェックが大切です。
製作スピードを上げるコツ
たとえば、試作品を頻繁に出力するような現場では、設計から出力までの流れをテンプレート化しておくと時短になります。 スライサーの設定をプリセット保存したり、使用頻度の高い部品は設計データをライブラリ化しておくと、毎回の作業がぐっと楽になります。
3.2 素材選びと造形方式の選定ポイント
3Dプリンターで部品を製作する際、どの素材を使うか、どの造形方式を選ぶかは非常に重要です。用途に合わない素材や方式を選んでしまうと、せっかく作ってもすぐに壊れてしまったり、思った性能が得られなかったりします。
素材と造形方式の選定ミスは、品質トラブルやコストの無駄につながる最大の原因です。
主な素材の種類と特徴
3Dプリンターでよく使われる素材には、それぞれ異なる特性があります。用途や使用環境に応じて、最適な素材を選ぶことが重要です。
PLA(ポリ乳酸)
初心者向けで扱いやすく、寸法安定性に優れています。ただし、熱に弱いため高温環境には不向きです。
ABS(アクリロニトリル・ブタジエン・スチレン)
強度があり、耐衝撃性も高め。工業部品によく使われますが、反りやすいので造形には工夫が必要です。
ナイロン
柔軟性と強度を兼ね備えた素材。ギアやヒンジなどの可動部品に向いています。
TPU(熱可塑性ポリウレタン)
ゴムのように柔らかく、衝撃吸収性があります。耐久性の高いパーツに使用されます。
レジン(光硬化性樹脂)
SLA方式で使われる液体素材で、精細な造形が可能。ただし、紫外線に弱く、屋外使用には注意が必要です。
素材選びの失敗例と対策
現場でありがちな素材選びのミスとその解決策を紹介します。
強度が足りず壊れやすい
→ 見た目で選んだPLAを使用し、機械的負荷に耐えられず破損。ABSやナイロンに切り替えることで改善できます。
反りや変形が発生する
→ ABSを加熱ベッドなしで使用すると、反りが起こりやすくなります。造形温度とベッド温度の管理が重要です。
後処理に手間がかかりすぎる
→ レジンを使った部品で、洗浄・硬化処理に時間がかかりすぎる場合があります。作業工数も含めて選定しましょう。
造形方式との相性を見極める
たとえば、細かい造形や美しい表面仕上げが求められる場合は、SLA方式+レジン素材の組み合わせが最適です。 一方で、強度と柔軟性が必要な機能部品には、SLS方式+ナイロン素材が適しています。
このように、「何を作るのか」「どこで使うのか」を起点にして、素材と造形方式をセットで考えることが成功のポイントです。
▶︎4. 3Dプリンター部品製作のコストと納期
4.1 コスト削減のポイント
3Dプリンターによる部品製作は、従来の加工方法に比べてコストを抑えやすい一方で、やり方を間違えると無駄な出費がかさむこともあります。材料の無駄、造形ミス、時間ロスなど、ちょっとした工夫で大きなコスト削減につながる部分が多く存在します。
適切な運用と設計の工夫で、コストを最大30〜50%削減することも可能です。
主なコスト構成と削減対象
3Dプリンターの製作コストは、大きく以下のような項目に分けられます。
材料費(フィラメント、レジンなど)
人件費(設計・出力・後処理)
稼働コスト(電気代、プリンター維持費)
失敗による再出力コスト
このうち、失敗回避や材料の節約によって、大幅なコスト削減が可能です。
よくあるコストの無駄と対策
以下のようなパターンで、無駄な出費が発生しやすくなります。
無駄なサポート材の使用
→ 設計時にサポートが必要な向きでモデルを作ってしまうと、材料が余分に消費されます。サポートレスの設計を心がけましょう。
出力失敗によるやり直し
→ スライス設定のミスや、温度設定の不備などが原因です。事前に小型のテスト造形を行うことで防げます。
オーバースペックな造形
→ 不必要に高密度・高解像度で出力してしまうと、時間と材料が無駄になります。用途に応じて設定を最適化しましょう。
設計段階でのコスト対策
たとえば、強度が求められない部分は中空構造にしておくことで、材料費を20〜30%カットすることができます。 また、分割出力によって造形範囲を狭め、時間短縮と材料節約の両立が可能です。
さらに、スライサーソフトの「インフィル密度」設定を調整するだけでも、内部充填量をコントロールできるため、材料の消費を大幅に抑えることができます。
4.2 納期短縮のための工夫
3Dプリンターの大きな利点のひとつが、必要なときにすぐ部品を製作できるスピード感です。しかし、造形ミスや工程の非効率があると、その強みが活かしきれません。
工夫次第で、設計から完成までの時間を40〜60%短縮することが可能です。
納期を守るためには、設計・データ処理・造形・後処理のすべてのステップにおいて、無駄を省く取り組みが重要になります。
納期を圧迫する主な原因
よくある納期の遅れには以下のような原因があります。
設計変更のたびにゼロからやり直している
→ 再設計のたびに最初からデータを作り直していると、時間が倍以上かかることもあります。
スライス設定に時間がかかりすぎている
→ 経験が浅いと最適な設定が分からず、試行錯誤に時間を取られがちです。
造形失敗による再出力
→ 造形中のエラーや造形物の剥がれによって、最初からやり直しになるケースが頻発します。
納期短縮のための具体的な対策
納期を短くするには、次のような工夫が効果的です。
設計データのテンプレート化
よく使う形状や寸法の部品は、テンプレート化しておくことで設計時間を短縮できます。
スライス設定のプリセット活用
一度うまくいった設定を保存しておけば、次回以降の設定に迷うことがなくなります。
同時造形・分割造形の活用
部品をまとめて一度に出力する、または大型部品を分割して短時間で出力し、後で接合する方法も有効です。
造形前のチェック体制の強化
事前に出力シミュレーションを行い、エラーや不要なサポートがないか確認することで再出力を防げます。
短納期が求められる現場での実感
たとえば製造現場で、ある治具が急に壊れてしまった場合、外注に出せば3〜5日かかることもあります。 ですが、社内で3Dプリンターを活用すれば、その日のうちに復旧できることも珍しくありません。
このような即応力は、生産ラインの安定稼働にとって大きなメリットとなります。
▶︎5. 3Dプリンター部品製作を依頼する際のチェックポイント
5.1 信頼できる業者の選び方
3Dプリンターを使った部品製作を外部に依頼する場合、どの業者に依頼するかは非常に重要です。安さや納期の速さだけで業者を選ぶと、品質に不安が残り、結果的に後悔することもあります。
信頼できる業者を選ぶことで、品質の高い部品を確実に提供してもらい、納期を守ることができます。
業者選びでチェックすべきポイント
信頼できる業者を選ぶために、以下のポイントを確認することが大切です。
過去の実績と事例
業者が過去にどのような部品を作ってきたかを確認しましょう。特に自分が依頼する部品に似た事例があれば、信頼度が高まります。
技術力と設備の充実度
3Dプリンターは種類が豊富で、性能や特性が異なります。業者が使用しているプリンターの種類や、その技術力が自分の要求に合っているかを確認しましょう。
品質管理体制
製造後の検査や品質管理がしっかりしている業者は、品質に対する意識が高いです。製品が基準を満たしているかを確認する体制があるかもチェックするポイントです。
納期の厳守度
業者が過去に納期を守っているか、もし遅延があった場合の対応について確認しておくことが重要です。納期が重要な場合、特に注意が必要です。
対応力とコミュニケーション
迅速で丁寧な対応をしてくれる業者は、トラブルや修正依頼に柔軟に対応してくれます。依頼から納品までの過程でスムーズにやり取りができるか確認しましょう。
5.2 見積もり依頼時の注意点
3Dプリンターを使った部品製作を外部に依頼する際、見積もりを取ることは非常に重要です。しかし、見積もりを依頼する際に気をつけるべきポイントを押さえておかないと、後で予算オーバーや納期の遅延が発生することもあります。
見積もりをしっかりと確認することで、予期しないコストや時間の無駄を防ぐことができます。
見積もり依頼時に確認すべきポイント
見積もりを依頼する際には、以下の項目を確認することが大切です。
部品の数量と単価
1点の部品に対してのコストだけでなく、量産する場合の単価を明確にしておきましょう。大量生産の場合、単価が安くなることがあります。
使用する素材とそのコスト
使用する素材の種類や量によって価格が大きく変動します。材料費が高額になることもあるため、素材ごとのコストを確認しましょう。
設計変更や追加作業の対応
見積もりには設計変更や追加作業が発生した場合の対応が含まれているかを確認しましょう。変更があった場合、追加費用が発生することがあります。
納期と納品のタイミング
納期が明確でない場合、後々トラブルに発展することがあります。納期を具体的に確認し、遅延のリスクを減らすために余裕を持った設定を依頼しましょう。
アフターサポートや保証内容
製品に不具合があった場合や、納品後のサポートが必要になる場合の対応も確認しておきましょう。アフターサービスの内容が不十分だと後で困ることがあります。
▶︎6. まとめ:3Dプリンター部品製作で製造業の未来を切り開く
3Dプリンターを活用した部品製作は、製造業において大きな変革をもたらしています。試作から量産、さらには最終製品の一部まで、幅広い分野での活用が進んでおり、これまでの製造方法では難しかった柔軟性やコスト削減、納期短縮などが実現されています。
3Dプリンターの導入により、製造プロセスが革新し、競争力の強化や市場への迅速な対応が可能となります。
3Dプリンター部品製作のメリット
コスト削減:金型や治具が不要で、少量生産でもコストを抑えることができます。
納期短縮:設計から製作までの流れがスピーディで、すぐに実物を確認できるため、製品の修正も迅速に行えます。
設計の自由度:複雑な形状や機能を持つ部品の製作が可能で、従来の製造方法では難しかった形状にも対応できます。
未来の製造業での活用
3Dプリンターは、今後ますます製造業に欠かせないツールとなっていくでしょう。特に以下の分野での活用が期待されています。
カスタマイズ製品の生産:顧客のニーズに合わせた製品を、オンデマンドで製作することが可能になります。
サプライチェーンの革新:部品の製作や補修がスピーディに行えることで、サプライチェーンが効率化されます。
持続可能な製造:リサイクル可能な素材を使った製造や、廃棄物削減にも貢献する環境に優しい製造方法として注目されています。
導入のポイント
3Dプリンターを活用するためには、適切な機材とソフトウェアを選定し、業者選びや見積もりの際に慎重に確認することが重要です。また、設計段階での工夫や、製作後のチェック体制を整えることで、トラブルを防ぎ、より良い部品を迅速に製作できます。
▶︎3Dプリンターで理想の造形を実現したい方へ
データ作成から出力まで、成功するためのポイントをしっかり押さえたガイドをご紹介します。
お困りの際は、ぜひ合同会社HANDAのサポートにお任せください。
Comments